随着工业生产技术的飞速发展,增材技术凭借其快速成型、生产周期短等特点,受到了越来越广泛的关注。增材制造(3D打印)作为一种新型金属制造技术,具有沉积速率快、成本低、制备过程简单、生成的结构件整体完整等特点[1]。增材制造技术作为目前先进制造技术的组成部分,已被各国作为现代产业发展的着力点之一。在高精度应用场景,由于其几何离散化的特点,每层表面质量缺欠和偏差将会累积构成整体结构件的偏差。正是因为其逐层累积的特点,打印过程中其表面有可能产生缺陷,而表面缺陷又被下一层粉末盖住,形成内部缺陷,内部缺陷的存在会影响零件抗疲劳性能和使用寿命[2]。因此,缺陷的检测对于保证增材制件的结构完整性和使用安全性尤为重要。
在缺陷形成原因方面,2007年,张凤英等[3]对增材制造缺陷的形成原因进行了相关研究,发现气孔的形成是材料特性造成的,与粉末的流动性以及含氧量无关;2012年,王黎等[4]发现粉末的粒度、粉末中氧含量对加工后的材料质量有很大影响。在缺陷检测方面,ZIÓŁKOWSKI等[5]和ZANINI等[6]采用CT检测技术对激光选区熔化制造的316L不锈钢零件以及Ti6Al4V试件中的孔隙率、孔隙尺寸及取向等进行检测。2016年,南昌航空大学的文艺[7]分析了两相(α+β相)钛合金的不同组织形态的力学性能差异,以及激光在不同成形方向上的材料性能变化,研究了3D打印两相钛合金缺陷类型和缺陷形成原因;并分别利用荧光渗透检测和超声C扫描检测技术检测出了3D打印两相钛合金的表面开口缺陷,以及内部的气孔、未熔合、夹杂缺陷。
近年来,随着各国对增材制造领域的不断投入,大量的无损检测方法已经应用于增材制件的检测。一些常用的射线、超声、涡流、红外热成像无损检测方法引起了科研工作者广泛的兴趣。目前在增材制造缺陷检测方面,射线检测被认为是最直观、有效的方法,其对气孔和夹杂缺陷具有很高的检出率,能够适应各类检测表面,并且检测结果可以达到亚毫米量级[8]。里斯本大学的LOPEZ等[9]利用X射线和超声检测技术检测了电弧增材制造(WAAM)的含有带孔、未融合、夹杂等缺陷的铝和低碳钢增材制件,并通过破坏性试验和液体渗透的方法加以验证。UHLMANN等[10]利用CT获得了未经热等静压处理的和经过热等静压处理的SLM制造的航空钛合金TiAl6V4试件的孔隙率,其中未经热等静压处理的试件孔隙率为3.05%,最大孔体积为0.024 mm3,经过热等静压处理的试件孔隙率减小至0.81%,最大孔体积减小至0.009 mm3。虽然射线检测精度较高,但对于裂纹缺陷,受照射角度的限制,无法检测出垂直照射的薄层缺陷,检测耗时长[11]。涡流检测可以实现非接触在线检测,TWI公司的RUDLIN等[12]在激光熔粉沉积镍基合金试件上制作人工缺陷并实施检测,试验结果表明,涡流检测对于直径小于0.2 mm的表面缺陷,以及1 mm深度处直径小于0.6 mm缺陷的检出率可达90%。KOBAYASHI等[13]使用涡流检测方法检测出了具有阶梯和斜度表面的增材制件内部直径为0.5 mm的圆孔缺陷,但涡流检测只能检测表面和近表面缺陷,且难以区分划痕和裂纹。超声检测可以实现对试件内部缺陷的检测,RIEDER等[14]首先将超声检测运用于增材制造的在线监测,结果表明,超声纵波波速随沉积厚度呈非线性变化,随着沉积厚度进一步增加,纵波波速趋向稳定。BELLOTTI等[15]使用基于二次谐波的非线性超声参数测定方法定量评估316L、304L不锈钢材料的位错密度,并使用线性超声对测量结果进行评估。ALBAKRI等[16-17]利用基于PZT传感器的声阻抗测量方法测量不同尺寸精度、不同位置精度、不同内部孔隙率增材制件的信号差异,随后又采用阵列的方式通过对比无缺陷和有缺陷试件的信号差异,实时在线监测增材制件加工过程中的不同层缺陷大小。除此之外,相控阵超声技术也被用于增材制件粗糙表面以及内部缺陷的检测。YANG等[18]使用电弧熔丝增材制造了钢试件,分别在不同层嵌入直径为1~3 mm的碳化钨球以模拟缺陷并作为相控阵超声全聚焦方法的校准,用于检测增材制件其他部位的未熔合缺陷尺寸。超声检测需要耦合剂,要求被检试件表面平整,虽然可以在基板背面安装超声探头,但是随着层厚增加,超声信号会逐渐减弱,因此超声检测很难实现对复杂构件以及较厚材料的检测。而激光超声具有长距离非接触、频带宽、快速检测等优势[19],文章利用激光超声纵波对增材制造缺陷试件进行检测,验证纵波在增材制造较薄试件中的传播性能,并采用变分模态分解(Variational mode decomposition,VMD)算法提高信号信噪比。
1. 检测方法
1.1 变分模态分解
VMD方法是一种非递归的信号分解方法,可以自适应地将振动信号分解为一系列的模态,每个模态都是基于中心频率与有限带宽滤波后的信号。该方法的实质是构造变分问题和求解变分问题[20]。
1.1.1 构造变分问题
构造变分问题的步骤为:① 对各模态信号进行Hilbert变换得到解析信号,以便获得信号的单边频谱;② 将预估中心频率混合到解析信号中,将各模态频谱调制到基频带;③ 对上述解调信号做高斯平滑处理,即计算梯度的平方L2范数。
则约束变分问题可以表示为
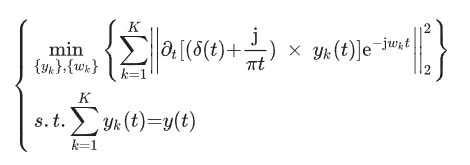
式中:k为分解的个数(k∈N+);yk为第k个模态,{yk}={ y1, y2, y3, ..., yk};wk为第k个模态的中心频率,{wk}={w1, w2, w3,...,wk}的集合。
1.1.2 求解变分问题
上述约束优化问题可使用二次惩罚因子α和拉格朗日因子λ(t)转化为无约束优化问题,其增广的拉格朗日表达式为
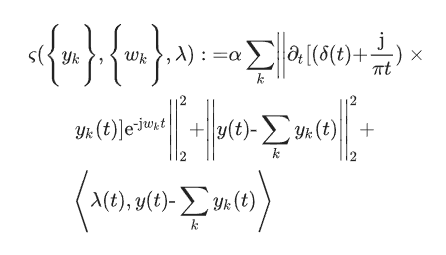
使用交替方向乘子方法求解式(2),即通过交替更新
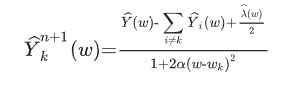
<math xmlns="http://www.w3.org/1998/Math/MathML">𝑦𝑘𝑛+1,𝑤𝑘𝑛+1</math>,λ(t)n+1求式(2)的鞍点。变分问题的解
<math xmlns="http://www.w3.org/1998/Math/MathML">𝜆^(𝑤)</math>分别为y(t),yi(t),λ(t)的傅里叶变换,式(3)中包含维纳滤波器结构,各模态时域信号可以通过对滤波后的信号做傅里叶逆变换取实部求得。
更新后的各模态中心频率为
VMD分解的具体步骤为:① 初始化<math xmlns="http://www.w3.org/1998/Math/MathML">{𝑌^𝑘1}</math>,<math xmlns="http://www.w3.org/1998/Math/MathML">{𝑤𝑘1}</math>,
<math xmlns="http://www.w3.org/1998/Math/MathML">{𝜆^1}</math>和n=0;② n=n+1,执行下一步操作;③ 由式(3),(4)更新
<math xmlns="http://www.w3.org/1998/Math/MathML">𝑌^𝑘</math>,wk;④ 由式(5)更新λ;⑤ 重复步骤②~④,直到满足
<math xmlns="http://www.w3.org/1998/Math/MathML">||𝑌^𝑘𝑛+1-𝑌^𝑘𝑛||22/||𝑌^𝑘𝑛||22<e</math>,输出各模态信号。
1.2 试验设备与试件
激光超声线源扫查系统实物如图1所示。该系统由YAG激光器、干涉仪、扫查架、激光扫查软件等构成。激光激励源通过振镜聚焦在增材制件有缺陷的一侧,干涉仪的光源聚焦在试件缺陷的背面,保持不动,进行对心接收。试验过程中,通过上位机的控制软件控制扫查架沿着x、y方向做弓字形移动。扫查架步进为0.3 mm,扫查区域尺寸(长×宽)为1.5 cm×1.5 cm,采集的数据点数为2 601,信号的采样频率为250 MHz,采样时间为10 μs,单个数据点数据长度为2 500。激光器的参数如表1所示。增材制造槽型缺陷试件及激光扫查方式如图2所示,该试件加工方式为激光选区熔化,材料为316L不锈钢,其尺寸(长×宽×高)为100 mm×50 mm×5 mm,在其正面中心位置加工了尺寸(长×宽×深)为2 mm×1 mm×1 mm的凹槽,在试件背面使用高能量的激光进行烧蚀,图中正方形区域即为烧蚀区域。当激光扫过缺陷时,激光产生的纵波信号到达干涉仪的距离减小,导致干涉仪接收纵波信号的时间提前、幅值增大,则通过观察纵波的传播图像,可以实现对材料缺陷的检测。
2. 试验结果
增材制件不同位置产生的激励纵波信号如图3所示,可以看出无缺陷位置的纵波最大峰值到达时间为1.836 μs,并且具有良好的可重复性;缺陷位置由于材料厚度减薄,纵波最大峰值到达时间为1.68 μs,信号幅度增大。在实际检测中,可以根据纵波最大峰值到达的时间差计算出缺陷的深度。对信号进行傅里叶变换得到的信号频域波形如图4所示,可以看出纵波信号频域成分较为丰富,频带分布范围广(集中在0 MHz~40 MHz),且激光在有缺陷处激励比无缺陷处激励得到的纵波信号频率幅值大。但是由于试验环境、电路、信号传输等多重因素的干扰,实际采集到的单次信号噪声较大。因此在后续处理过程中需要对信号进行过滤,挑选有用信息进行分析。
对无缺陷处信号进行VMD分解,结果如图5所示。在分解过程中根据信号频域信息,0~20 MHz为信号频率的第一个波峰到波谷,20 MHz为频域信号第二个波峰出现的位置,40 MHz以后信号的频率幅值较低,因此在VMD分解过程中设置其IMF分量的个数为3,并适当设置其平衡参数σ在[1 000,20 000]内变化,当σ=2 000时,信号分解结果满足以上要求。经过VMD分解后信号被分解为3个IMF分量,其中IMF1分量噪声较小,且最接近于激光超声原始信号,因此选择IMF1进行分析,得到信号的一次纵波信号最大峰值及二次纵波最大峰值信号。缺陷处信号的VMD分解结果如图6所示,通过对比发现,缺陷处IMF1分量的一次纵波、二次纵波到达时间比无缺陷处的早,且幅值高。在频域中缺陷处信号的频域幅值普遍比无缺陷处的高。有无缺陷处的VMD分解后信号时域及频域图对比如图7所示。
x轴的B扫描成像结果如图8所示。对比图8(a),(c)可知颜色最深位置偏移处的色带为纵波越过缺陷时干涉仪采集到的信号。测量得到此位置处的色带长度分别为1,2 mm,图8(b),(d)的颜色更深,成像结果更加清晰。
增材制件原始信号的C扫描成像结果如图9所示,其中红色部位为缺陷信号,测量得到图9(a)中缺陷尺寸(长×宽)约为1 mm×1.8 mm,图9(b)中缺陷尺寸(长×宽)约为1 mm×2 mm,该结果与原始缺陷尺寸基本吻合。在y轴4.5~15 mm处可以看到不同颜色的痕迹,即增材制件背面的烧蚀区域。
3. 结语
文章利用激光超声技术对增材含缺陷试件进行检测,并采用VMD算法对缺陷信号进行降噪,明显提高了缺陷信号识别度,从而提高了检测精度。通过A扫描信号可以发现纵波在增材制造厚度为5 mm的试件上具有较好的穿透性,即纵波可以较好地检测较薄试件的表面缺陷。增材制件在加工过程中,处于高温状态,而激光超声具有长距离非接触、频带宽等优势,因此文章结果可以为增材制件的在线检测奠定基础。